A Practical Methodology for Meeting ISO 26262 Random Faults Safety Goals in Automotive Semiconductor Products
In this article, we present a simple, easy step-by-step methodology to comprehend and achieve functional safety from random faults based on Questa® simulation and the fault-injection accelerator from Optima.
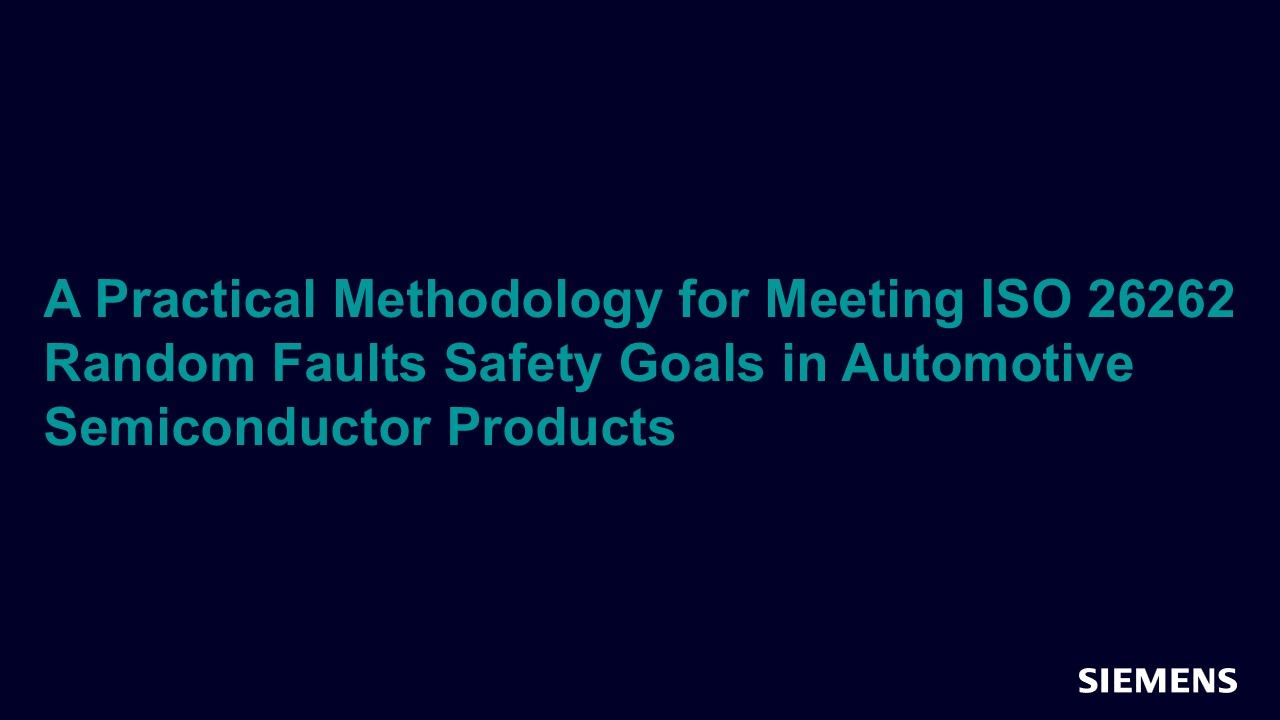
Full-access members only
Register your account to view A Practical Methodology for Meeting ISO 26262 Random Faults Safety Goals in Automotive Semiconductor Products
Full-access members gain access to our free tools and training, including our full library of articles, recorded sessions, seminars, papers, learning tracks, in-depth verification cookbooks, and more.