ISO 26262 Fault Analysis – Worst Case is Really the Worst
Imagine you’re a verification engineer being asked to get a small 10K gate design ISO 26262 certified. Assuming you don’t take the smart decision to quit your job, what would be your first step? If you would have been asked to do plain functional verification of the design, it is obvious you would start by reading the DUT spec.
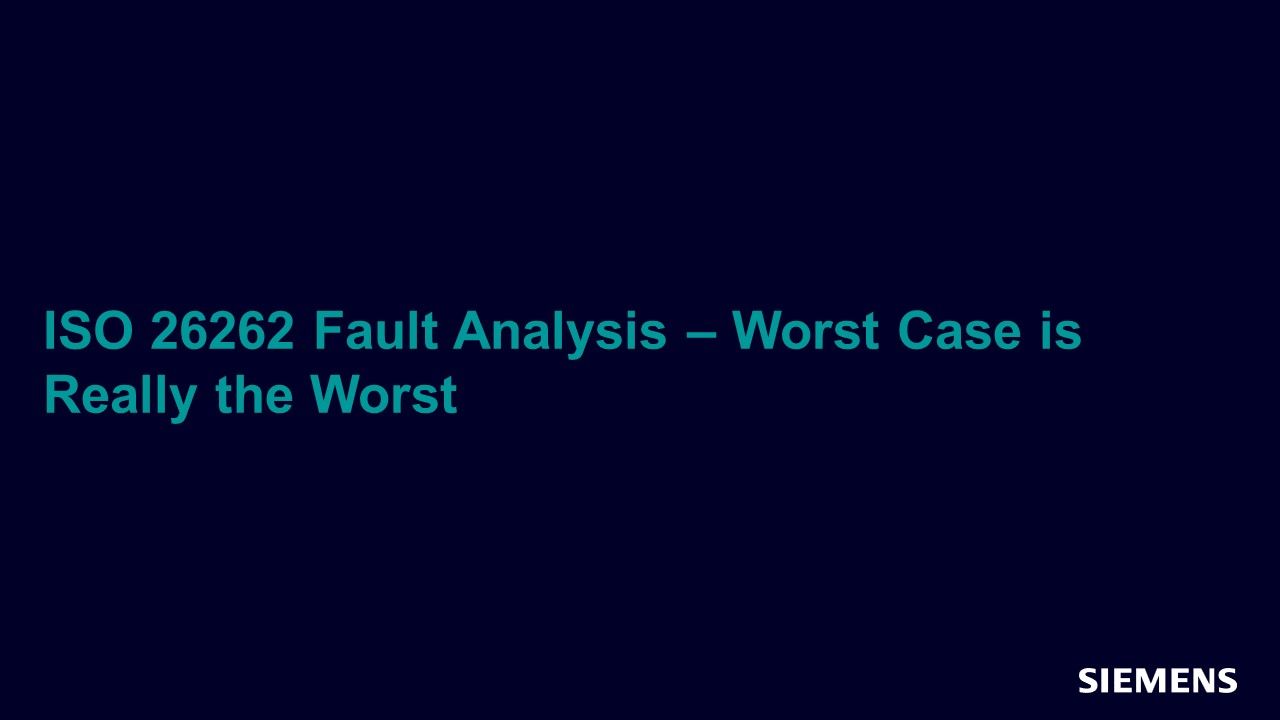
Full-access members only
Register your account to view ISO 26262 Fault Analysis – Worst Case is Really the Worst
Full-access members gain access to our free tools and training, including our full library of articles, recorded sessions, seminars, papers, learning tracks, in-depth verification cookbooks, and more.