Minimizing Constraints to Debug Vacuous Proofs
Most false positives (i.e. missing design bugs) during the practice of model checking on industrial designs can be reduced to the problem of a failing cover. Debugging the root cause of such a failing cover can be a laborious process, when the formal testbench has many constraints. This article describes a solution to minimize the number of model checking runs to isolate a minimal set of constraints necessary for the failure. This helps improve formal verification productivity.
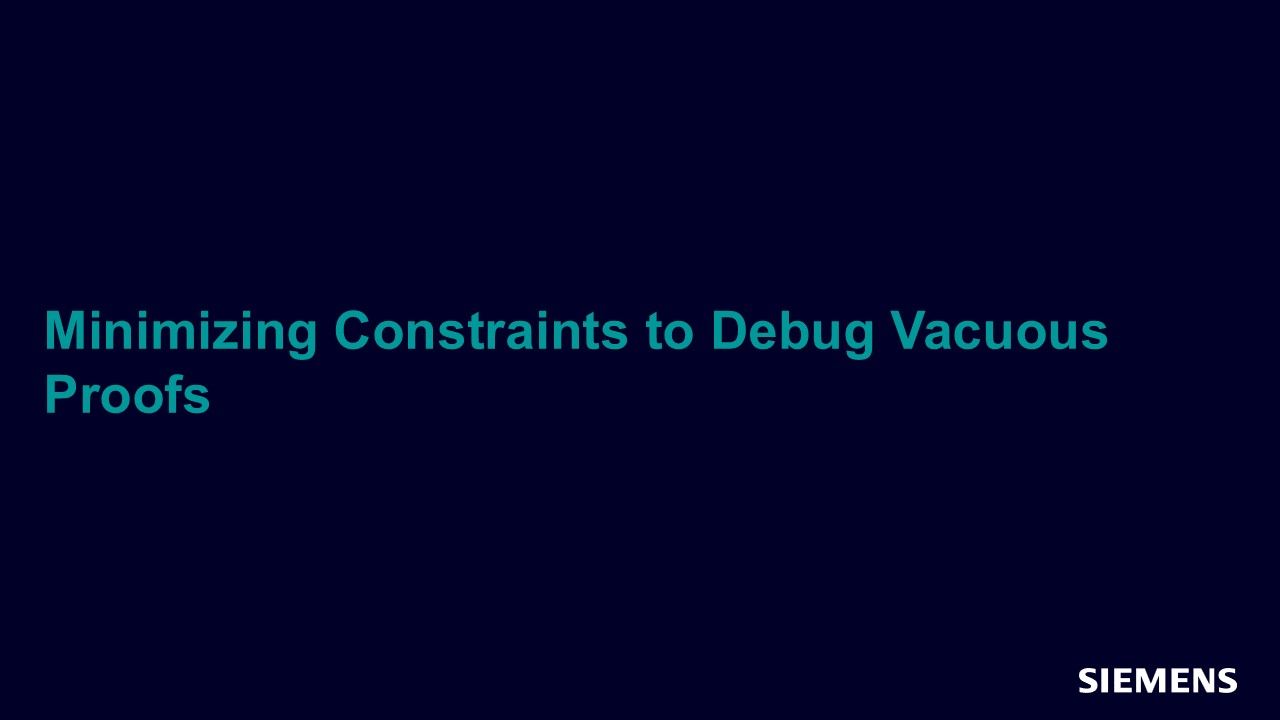
Full-access members only
Register your account to view Minimizing Constraints to Debug Vacuous Proofs
Full-access members gain access to our free tools and training, including our full library of articles, recorded sessions, seminars, papers, learning tracks, in-depth verification cookbooks, and more.