RTL Glitch Verification
It is important that certain timing endpoints on a design are safe from glitches. For example, it is necessary that an asynchronous reset never have a glitch that momentarily resets a flop. It is also necessary that multi-cycle paths are safe from glitches, i.e., it should not be the case that while a cycle accurate simulation of the RTL shows correct multi-cycle behavior, once delays are accounted for a glitch can propagate along the path resulting in a single-cycle path.
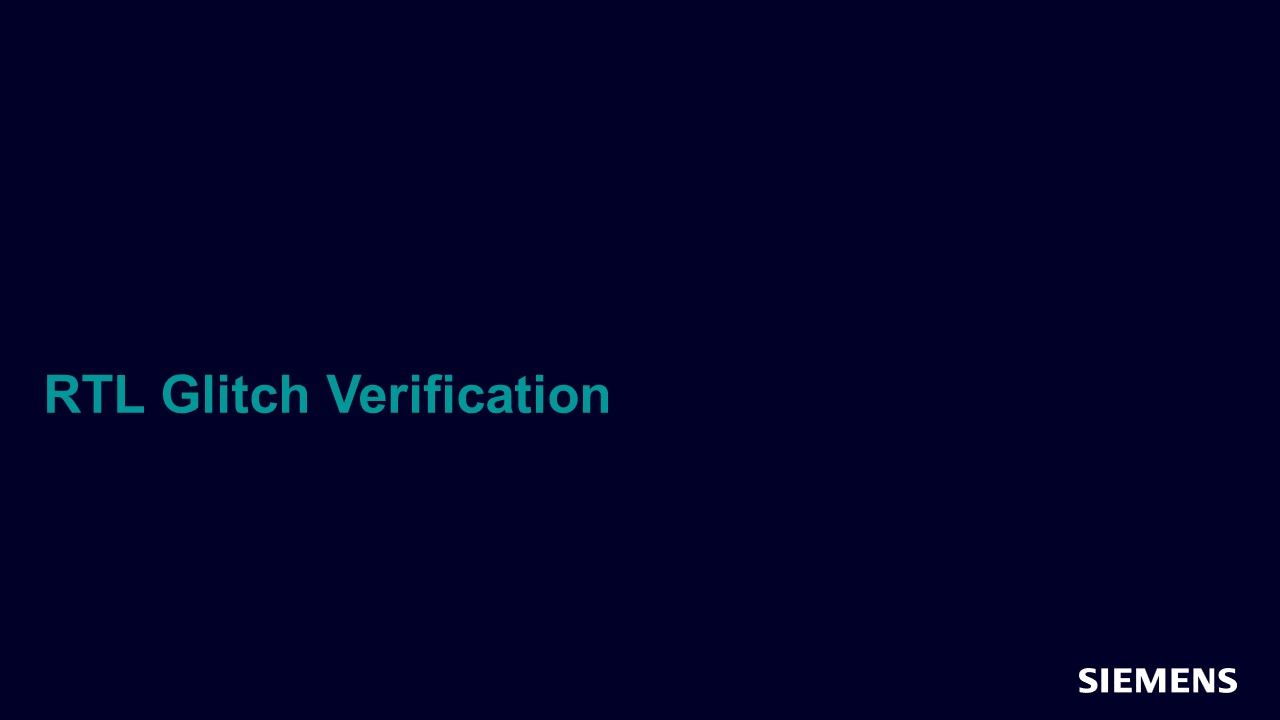
Full-access members only
Register your account to view RTL Glitch Verification
Full-access members gain access to our free tools and training, including our full library of articles, recorded sessions, seminars, papers, learning tracks, in-depth verification cookbooks, and more.