Emulation Based Approach to ISO 26262 Compliant Processors Design
This article reviews the use of processors in the automotive industry, the origin of faults in processors, architectures of fault tolerant processors and techniques for processor verification with fault injection.
We then propose an emulation-based framework for performing fault-injection experiments on embedded processor architectures.
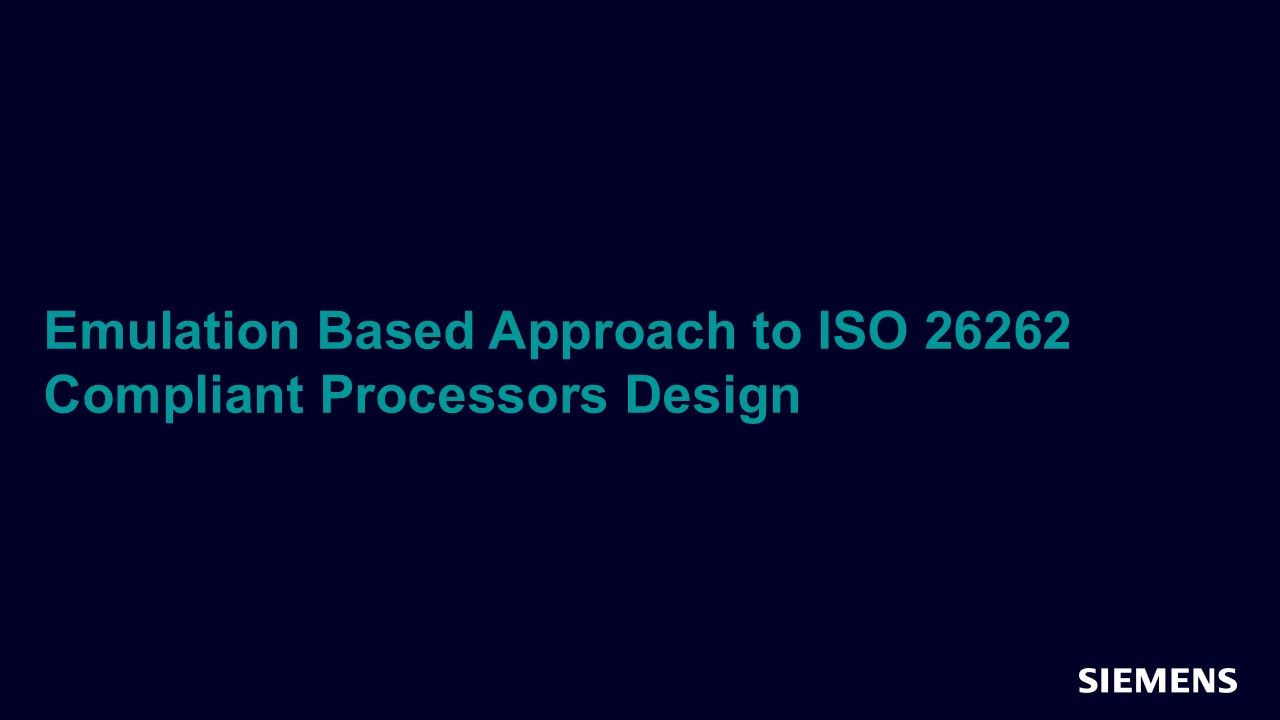
Full-access members only
Register your account to view Emulation Based Approach to ISO 26262 Compliant Processors Design
Full-access members gain access to our free tools and training, including our full library of articles, recorded sessions, seminars, papers, learning tracks, in-depth verification cookbooks, and more.