Effective Validation Method of Safety Mechanism Compliant with ISO 26262
The metrics to measure the effectiveness of Safety Mechanisms include code coverage rate, SPFM (Single- point failure metric) and LFM (Latent failure metric). Especially in SPFM and LFM, if the specified value is not reached on the Fault Injection Simulation (using Gate Level) at the end of verification, it will cause iterations, which will cause a significant increase in time and cost compared to consumer LSIs.
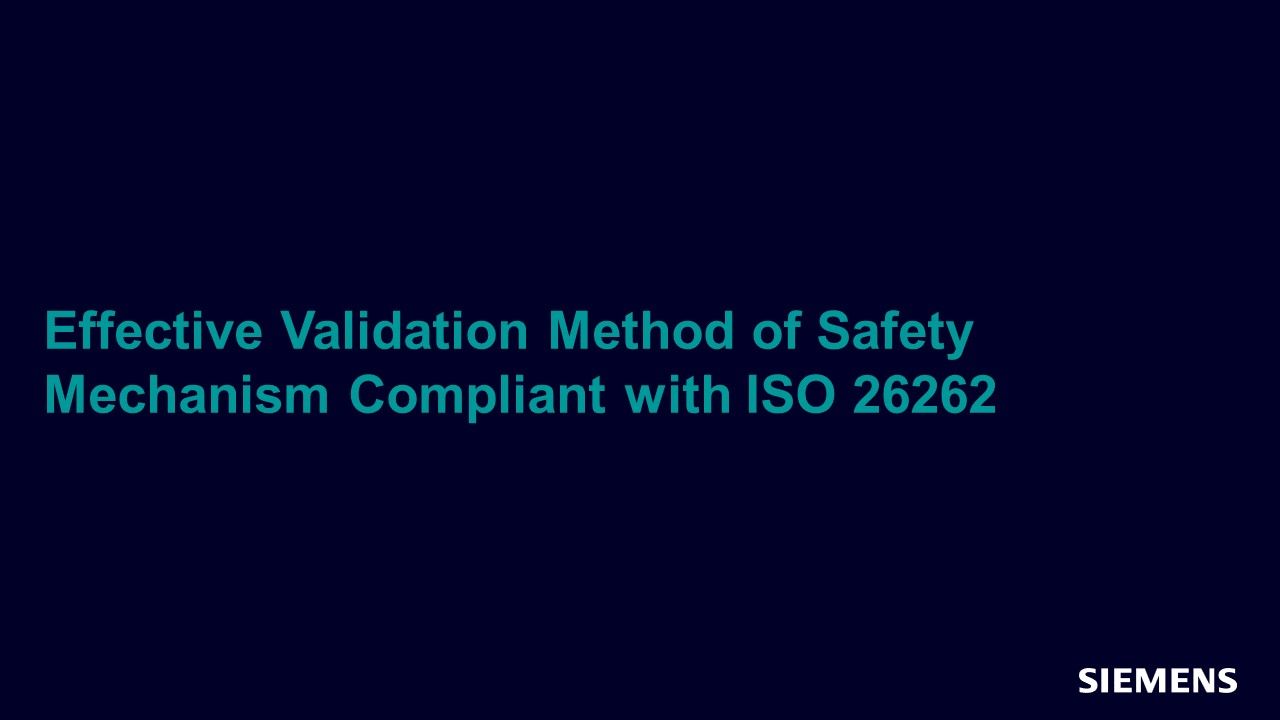
Full-access members only
Register your account to view Effective Validation Method of Safety Mechanism Compliant with ISO 26262
Full-access members gain access to our free tools and training, including our full library of articles, recorded sessions, seminars, papers, learning tracks, in-depth verification cookbooks, and more.