An End-to-End Functional Safety Solution for Automotive ICs Based on ISO 26262
In this webinar, you will learn more about Siemens EDA functional safety concepts and tool flow. In addition, we will walk you through our closed-loop solution; from requirements gathering, FMEDA, safety analysis, fault injection and back to merging the results to generate the work products necessary for certification.
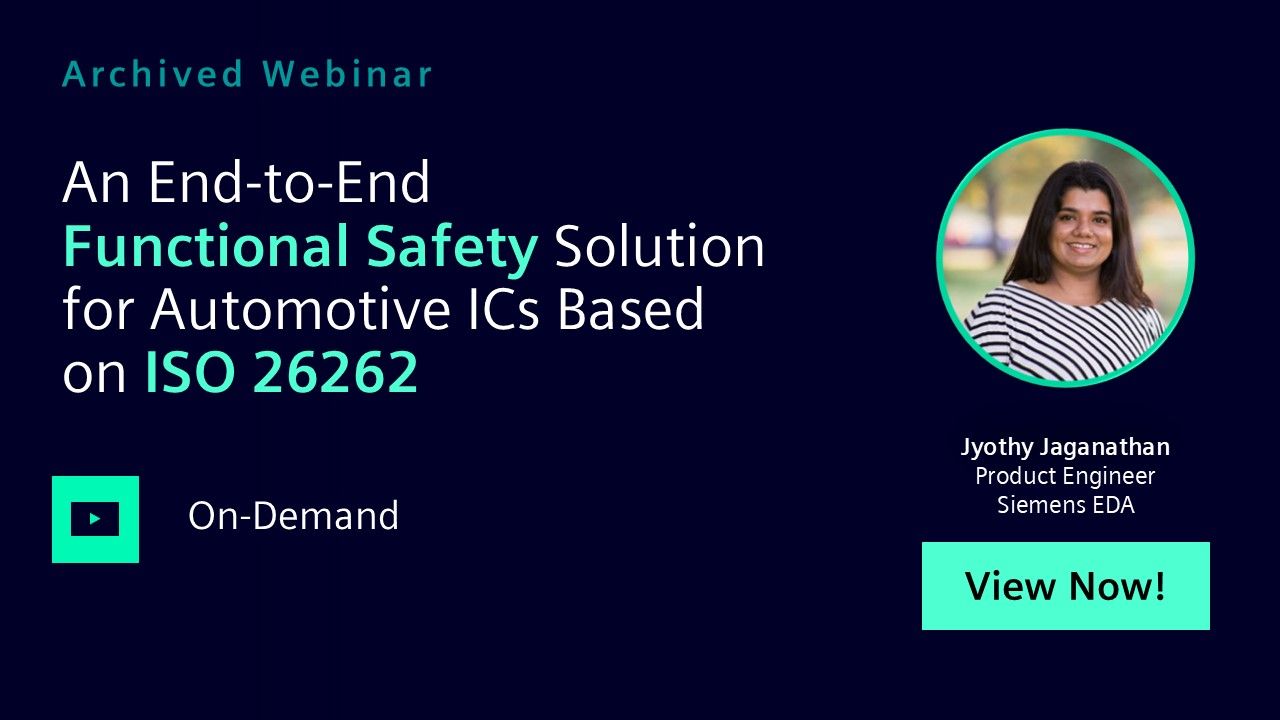
Full-access members only
Register your account to view An End-to-End Functional Safety Solution for Automotive ICs Based on ISO 26262
Full-access members gain access to our free tools and training, including our full library of articles, recorded sessions, seminars, papers, learning tracks, in-depth verification cookbooks, and more.